EuroSteel Finishes
“Design is where science and art break even.” — Mieke Gerritzen
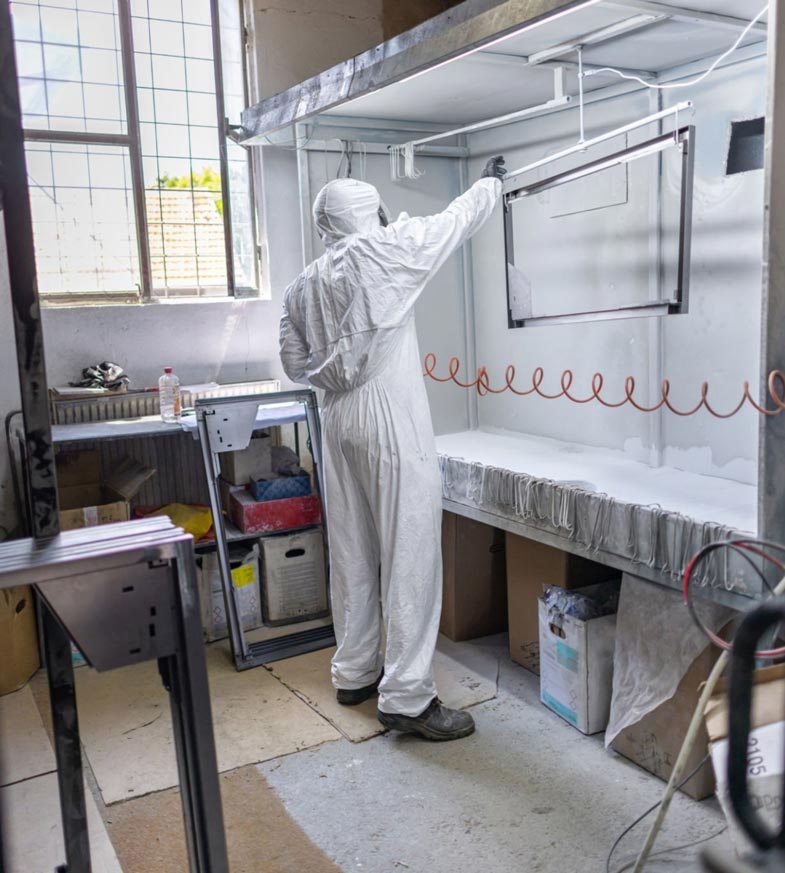
Zinc Galvanized Steel
Zinc galvanizing is by far the most effective way of protecting steel from corrosion. Many companies claim that they alone do this, but it is a standard procedure for protecting steel. What varies is the method and number of layers of zinc, plus the subsequent layers of finish and system of curing.
All our raw steel is ‘Zinc Electro Plated’ before it goes into production. This is to protect it from corrosion during fabrication. After fabrication is complete, all surfaces are sand blasted in preparation for a second Thermally Applied layer of zinc. Thermal spraying is a most effective and proven method of corrosion prevention, giving the steel galvanic, as well as barrier coating protection. In this process, the molten zinc metal bonds with the steel, both physically and chemically. To our knowledge – no other steel company applies 2 layers of zinc. The resulting surface is slightly rough, providing an optimal “key” for subsequent priming and surface finishing.
Our proprietary 9 stage process incrementally bakes in protection as it hardens and refines the surface.. From years of experience, we know that when steel is treated in this way, it will outlast and out perform any other fenestration material.
EuroSteel 9 Stage Finishing Process
- All raw material is Zinc Electroplated before being processed.
- Flame applied Zinc galvanization applied after fabrication.
- A layer of base priming is applied & baked on.
- Filler coat is applied, with sanding to create a smooth surface.
- Two layers of undercoat are applied for color depth & increased protection.
- Units are oven baked at 140º C to bond all sub layers and harden the surface.
- Application of topcoat, with choice of final color or patina.
- Two applications of Clear ‘Hard as Nails’ finish with a soft, 15% sheen.
- Final oven baking at 140º for a permanent maintenance free surface.

Marine Grade Finish
EuroSteel Architectural uses AkzoNobel marine coatings, which have been protecting ships for over 230 years! This product has superb protective qualities with superior abrasion and chip resistance. Our ‘marine grade’ finish protects steel from scratches, dents or other damage that commonly affects all other types of fenestration.
Gradual Layering
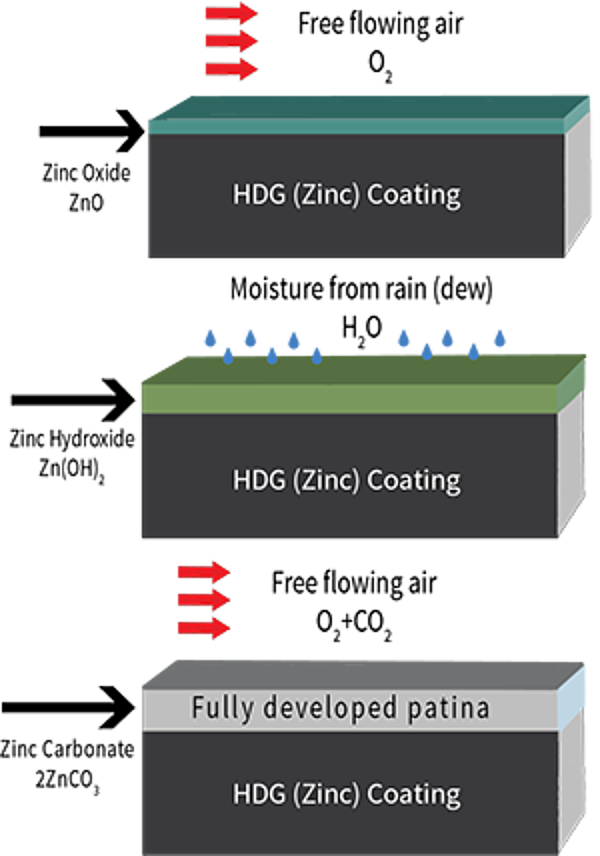
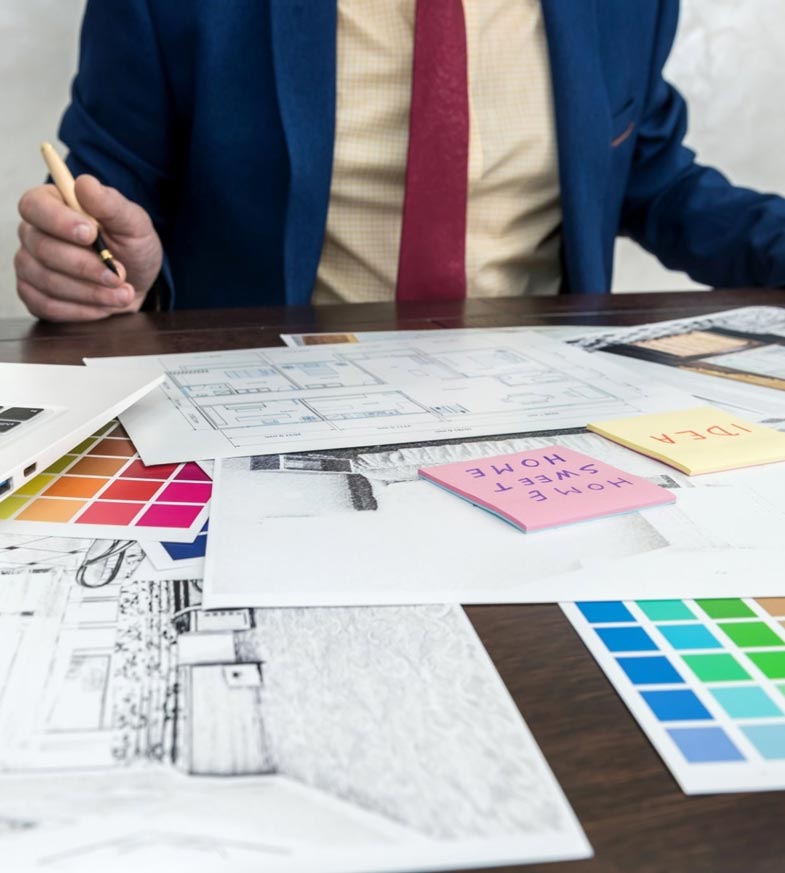
Color Choices
While the majority of our clients prefer the traditional look of black steel frames, you can have any color you wish. Black has been preeminent throughout the centuries, since steel became a primary material for building. However, we can match any color, working from a sample or Pantone number. We can also create a patina finish which adds texture and gives the product a living character and a hint of warmth. Creating a patina requires a truly artistic craftsmen who applies layers of contrasting or metallic color that picks up the edges and features of the metalwork, creating a totally unique look. Patinas are usually featured on exterior doors where there are iron embellishments that ‘show off’ the beauty of the patina. Please let your EuroSteel project manager know if you’re interested in exploring a patina finish. Otherwise, the steel frames for your doors and windows will be treated with traditional and elegant 15% sheen black.
Aluminum Anodizing
Aluminum is strong and lightweight but, like most metals, highly susceptible to corrosion and wear. To prevent this, EuroSteel Architectural utilizes Type III – Hardcoat Anodizing – the most comprehensive treatment of aluminum available. This process produces a much thicker coating than Type II anodizing, due to the higher voltage applied, longer bath immersion time and lower bath temperature. This coating is harder than tool steel, highly durable, resistant to salt water spray, abrasion and scratch resistant. The color of your choice is dyed in during the anodizing process so it will not flake or peel off. Anodized aluminum is also highly resistant to UV fading from exposure to sunlight.
Matched Finishes
Hot/Cold Rolled Steel
Some companies make much of the fact that they use cold rolled steel and frankly, it’s a non-issue. Almost all companies who make windows and doors use cold rolled steel because it is the superior product. The difference between the two steels is that Hot Rolled steel is rolled to its final dimensions while hot, whereas a cold rolled product can be finished to much closer tolerances right in the sizing rollers. The cold rolling process produces steel with much higher strength and hardness than the steel produced by the hot rolling process. Hot rolled steel tends to have very rough surfaces whereas cold rolled steel has a shiny and smooth surface that allows it to be used as-is in production operations. These two steel types should not be confused with the technical specifications or grades used to classify steel by composition or physical characteristics. EuroSteel uses the highest grade of steel manufactured for the stress and demands of this type of building. C25.fhipv